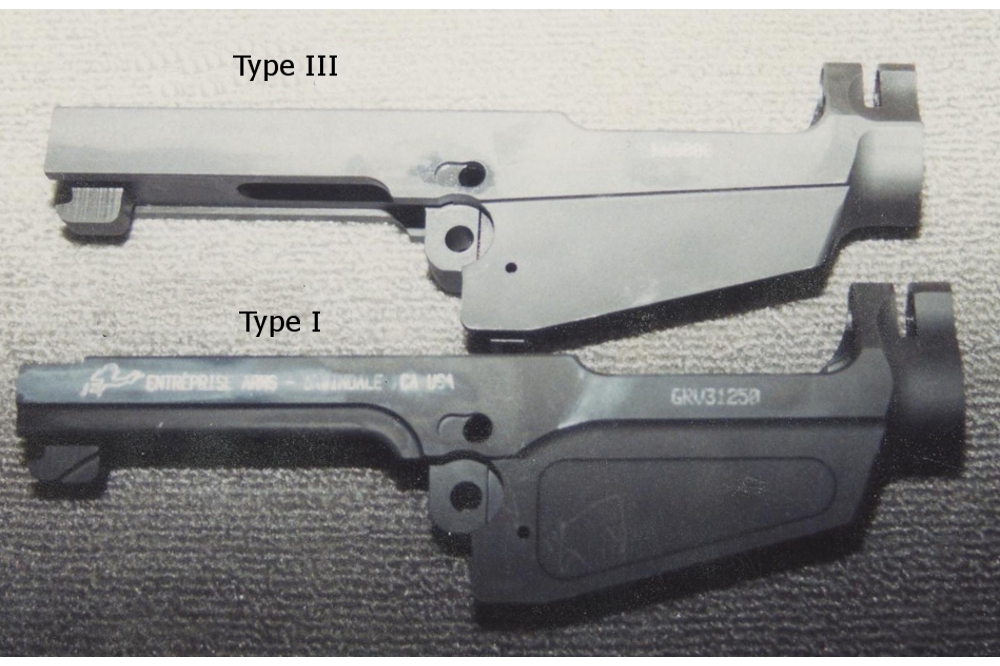
FAL Review: Entréprise Arms Inc. FAL Receiver
In light of my unabashed criticisms, I was particularly surprised to get a call from Lawrence Abbot at Entréprise around Thanksgiving of 1999 asking me if they could send me some free samples of their parts and receivers for evaluation. Lawrence apparently had taken over quality control responsibilities and found that indeed my comments did have merit. He oversaw changes that might improve the quality of the product – hopefully turning it into something that could be assembled without significant modifications to both the receiver and the “in spec” parts kit. Coupled with an alleged interest in improving their customer service reputation, Walt and Lawrence actively solicited feedback from the FAL building community and claim to have made substantial headway in redressing customer complaints.
I received the receivers, a Type I (GRV 28779) and a Type III (KR3615) on January 17, 2000. I began my evaluation with careful photographic documentation, which demonstrated serious problems with the font magazine notch, barrel timing, and feedramp geometry. Lawrence admitted these receivers were defective and issued a call tag for their return before I had completed my evaluation. I don’t know if they sold any of this production run to others, and if they did, if they recalled those as well.
The replacement Type I and Type III were noticeably improved in the areas I had observed in the first samples. Follows a photographically documented review of the Type I and Type III Entréprise receivers.
This is an older review, where neither my photographic skills, nor equipment, are what they are today.
The Type I has all the appropriate weight reducing (“lightening”, not “lightning”) cuts and sand cuts on the inside. In theory, the bolt carrier will push debris into these cuts so as to keep the debris from affecting operation. Additionally, a Type I is approximately 3.5 ounces lighter than a Type III.
It is interesting to note also that this second receiver required a spanner wrench for the last 4 turns. I could have chased the threads (9/16×24 RH) but wanted to see how much effort was going to be required. The front of the Type I has the correct radius and lightening cuts.
(followup: Lawrence claims this is not a problem as it does not affect function and he claims to have fixed it).
The extractor relief cut had rough serrations, as was the cut on the opposite side. The receiver the bridge is wavy. I couldn’t photograph the underside of the bridge, but it too was off. It is supposed to be flat – it cams the front of the bolt down. These had an irregular double-bevel. There is supposed to be a radius on the right side for the extractor to cam outward, and a smaller one on the left, but you can see the center section is not flat either. This does not appear to affect operation.
The photograph that did not turn out well was a closeup of the feedramps. The radii are either too deep or too close together, as the ridge in the middle is smaller than on an FN receiver. This does not seem to have an adverse effect on operation. The same closeup showed the front recess for the tab on the front of the magazine. It is taller and wider than an FN, but works. One gun fit all magazines loosely. It still cycled fine, and perhaps its simply a stacking of errors with a worn mag catch and a pile of used magazines, but it also could be this notch was a bit too low.
This fit is crucial to accuracy as the front sight is on the upper and the rear sight is on the lower. Any slop between the two affects the relationship between the front and rear sight, and therefore accuracy.
The Type III hand-timed even shorter, but this is not unusual and a lot better than over-timing. I am concerned about the thread engagement, as there was considerable lateral play prior to snugging against the shoulder. I do not consider it a safety issue.
Both guns headspaced in what I consider an average range, that is .256″-.260″ locking shoulder.
Follow-up Lawrence told me this was to prevent locking shoulder “setback” an event where the locking shoulder presses back against the receiver during firing, increasing the headspace slightly. I describe this process more completely in “Gunplumber’s Guide to FN FAL Home Gunsmithing.” I don’t buy it. FN contract guns are built with a tight initial headspace to compensate for this phenomenon, which only occurs during the first few rounds.
Follow-up Lawrence claimed that they pulled 10 receivers at random and assembled them into complete rifles in 20-30 minutes each, and experienced no such problems. All guns functioned flawlessly. I don’t know what to say other than I am skeptical. It takes me longer than that just to clean, inspect, and prepare the parts. I consider his claim to be dubious at best.
The first gun was uneventful. No malfunctions. I did not shoot for group, but could bounce a gallon milk jug up a 10 meter incline at approximately 100 meters from the shoulder. The second gun also cycled 6 magazines of mixed ammo without a hitch.
Follow-up Lawrence was not pleased with my evaluation. While finding no fault in its technical accuracy, he kept saying that it would “hurt our relationship” and he has since removed me from their list of “recommended gunsmiths.” In retrospect, it appears that the receivers were not “no strings attached” as he originally claimed, but a bribe to revise my earlier comments.
He obviously didn’t know me very well. I have too big an ego to give other than a clear, objective, carefully documented evaluation. He then had the gall to then send me a bill for the “free”: receivers, but when I sent him a bill for my many hours of careful review and photographic documentation, he tried to sue me.
Given what I consider extremely unethical behavior, I now have zero trust or confidence in the company or their representatives, and am not interested in purchasing or working on their products.
Leave a Reply
You must be logged in to post a comment.